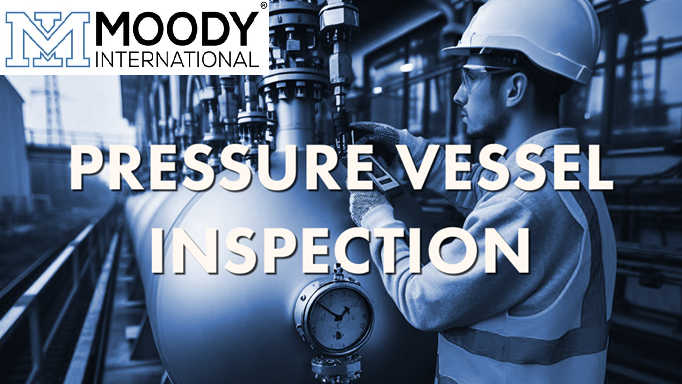
BOILER & PRESSURE VESSELS INSPECTION
Independent Certification and Inspection of Pressure Vessels
Boilers and pressure vessels are used all over the world in different industries including oil and gas and energy industries. To ensure the safety and operational efficiency of pressure vessel equipment, certain regulations and codes have been developed, some of which require independent inspection and certification to achieve compliance.
Companies and professionals involved in the fabrication, installation, inspection, or repair of boilers and pressure vessels must adhere to the regulations provided by the Boilers & Pressure Vessels Regulation. This applies to all steam-generating units, with very few exceptions. The standards have been drafted to help ensure public safety and minimize risk from incidents due to negligent practices when working with boilers and pressure vessels.
Statutory Obligations Features
The Boilers & Pressure Vessels Regulations list certain statutory obligations that must be adhered to by all relevant parties. These include the testing, examination and certification of boilers and pressure vessels according to the standards laid out by the government agency responsible for their regulation. All certifications issued by these officials are considered valid until their expiration dates, which must not exceed 1 year. Additionally, all plants should review their policies and procedures regularly to ensure they remain up-to-date with any changes or modifications in the law or regulations concerning boiler safety.
Types of Inspections
An inspection of boiler and pressure vessels is classified into three types: 1) pre-service; 2) periodical; and 3) special inspections. Pre-service inspections must be completed before a brand new boiler/pressure vessel is used; whereas periodical inspections should be carried out regularly during the operation of the boilers/pressure vessels in order to identify equipment failures, performance issues, and potential safety problems. Special inspections are conducted when an unexpected incident occurs – such as a possible gas leakage – or when changes in technology make it necessary. All three types of inspections must comply with the legal requirements listed in the Boiler & Pressure Vessels Regulations.
Advantages of Boiler & Pressure Vessels Legislation
Boiler & Pressure Vessels Legislation has a number of advantages, including the following: it ensures that maintenance is properly carried out and monitored; provides guidance on the installation, use, and disposal of boilers/pressure vessels; offers comprehensive safety guidelines to prevent malfunctions, gas leaks, and explosions; encourages the use of up-to-date technology in order to increase efficiency. Furthermore, this legislative framework also serves as a way for manufacturers and operators to bridge their responsibilities with regard to boiler/pressure vessel pressurization.
Benefits of Our Boiler and Pressure Vessel Inspection Services at a Glance
Moody International boiler and pressure vessel inspection services offer:
• Qualified experts with extensive experience in certifying pressure equipment and related components. • Assistance in preparing your products for exporting abroad. • Global customer service with quick response times for all needs. • Expert knowledge of different regulations, standards and codes.
WELDERS QUALIFICATION CERTIFICATION
Energy projects and metal constructions require fully trained and highly level staff. The Moody International Assurance Limited Body adapts these requirements and organizes 7 Major Qualification & Certification Tests for all the welding activities:
Certified Welder according to EN 14732 – (CW14732/XXX)
Certified Welder according to ISO 9606 – (CW9606/XXX)
Certified Welder according to ISO 13585 – (CW13585/XXX)
Certified Welder according to ISO 15618 – (CW15618/XXX)
Certified Welder according to EN 13067 – (CW13067/XXX)
Certified Welder according to AWS – (CW-AWS/XXX)
Certified Welder according to ASME Section IX, article 3 – (CW-ASMEIX/XXX)
Certified Welder according to EN 14732 – (CW14732/XXX)
Qualification testing of welding operators and weld setters for mechanized and automatic welding of metallic materials
ISO 14732:2013 specifies requirements for the qualification of welding operators and also weld setters for mechanized and automatic welding.
ISO 14732:2013 does not apply to personnel exclusively performing loading or unloading of the automatic welding unit.
ISO 14732:2013 is applicable when qualification testing of welding operators and weld setters is required by the contract or by the application standard.
Certified Welder according to ISO 9606 – (CW9606/XXX)
Qualification testing of welders — Fusion welding
ISO 9606-1:2012 specifies the requirements for qualification testing of welders for fusion welding of steels. It provides a set of technical rules for a systematic qualification test of the welder and enables such qualifications to be uniformly accepted independently of the type of product, location and examiner or examining body. When qualifying welders, the emphasis is placed on the welder’s ability manually to manipulate the electrode, welding torch or welding blowpipe, thereby producing a weld of acceptable quality. The welding processes referred to in ISO 9606-1:2012 include those fusion-welding processes which are designated as manual or partly mechanized welding.
Certified Welder according to ISO 13585 – (CW13585/XXX)
Qualification test of brazers and brazing operators
ISO 13585:2012 specifies basic requirements for the qualification testing of brazers and brazing operators providing conditions for brazing, testing, examination, acceptance criteria and range of qualification for certificates. • brazer ability to by hand manipulate the device for heating following a specification to reproduce a braze joint with acceptable quality” • operator ability to follow a specification to reproduce a braze joint with acceptable quality”
Certified Welder according to ISO 15618 – (CW15618/XXX)
Qualification testing of welders for underwater welding
This standard applies to welding processes where the skill of the diver-welder or welding operator has a significant influence on weld quality.This standard specifies essential requirements, ranges of approval, test conditions, acceptance requirements and certification for the approval testing of diver-welder or welding operator performance for the welding of steels underwater in a hyperbaric dry environment.
Certified Welder according to EN 13067 – (CW13067/XXX)
Qualification testing of welders. Thermoplastics welded assemblies The standard specifies the method for assessing the knowledge and skills of a welder who is required to weld thermoplastic materials in new construction and repairs. The distribution companies, gas and water with qualification programs alternative are excluded from this rule. The standard applies to the following welding processes: • Hot gas welding: nozzle with round, high-speed nozzle, with the wedge; • Extrusion welding; • Welding tool hot: head to head, saddle, glass, wedge; • Electrofusion welding: glass, saddle; • Chemical welding (bonding): glass. The standard applies to the welding of the following products: • Plates; • Tubes; • Fittings; • Membrane coating.
Certified Welder according to AWS – (CW-AWS/XXX)
AWS Performance Qualification Test
This Supplement to the AWS QC7-93, Standard for AWS Certified Welders, provides a welder certification method not specifically based on a code but which may be acceptable for various codes. The rules for performance qualification are as defined by the applicable specification referenced in the WPS or as defined by the employer in the WPS or accompanying documentation (acceptance criteria). The administrative rules for the American Welding Society (AWS) Certified Welder Program are provided in AWS QC7-93. Test facilities participate in the program are required to meet the provisions of AWS QC4, Standard for Accreditation of Test Facilities for AWS Certified Welder Program. Neither AWS QC7-93, nor this supplement prevents or supersedes a manufacturer or contractor from continuing to qualify welders in accordance with other standards or procedures.
Manufacturers or contractors may impose. Supplementary requirements to this standard as deemed necessary.
Certified Welder according to ASME Section IX, article 3 – (CW-ASMEIX/XXX)
Welding Performance Qualifications QW-300
Article III covers the preparation of WPQ records. Each welding process is listed separately in QW-350 with the essential variables for welding performance. The WPQ form must record a value for each essential variable used and must list a range qualified for each of these essential variables.
Article III covers responsibility, type of tests, records, welder identification, positions, diameters, expiration and renewal of qualifications. Welders and Welding Operators may be qualified by visual and mechanical tests, or by radiography of a test coupon, or by radiography of the initial production
Requirements for an Official Examination Certificate
To obtain an official examination certificate, the boiler/pressure vessel must pass an inspection by either a professional engineer or a certified inspector. This is done for the purpose of determining whether or not the component is built to national standards and operating safely. The examination also includes checking components for any signs of undue corrosion and wear. In addition, measurements are taken to verify that internal and external surfaces are adequately smooth and in good condition. Upon successful completion of the evaluation, a Certificate with inspection details will be issued by the authorized personnel in charge.
Why MOODY:
Are you in need of a quick and reliable Inspection of Boiler and pressure vessels? Our experienced inspectors are qualified and accredited to perform a wide range of inspections according to international standards. In many places across the globe, our inspectors can be on-site within 72 hours. You also have the option to add a video of your inspection for another layer of authentication. • Fast, Flexible and Transparent • Local Expertise • In-House and Accredited Technicians • Personalized Service